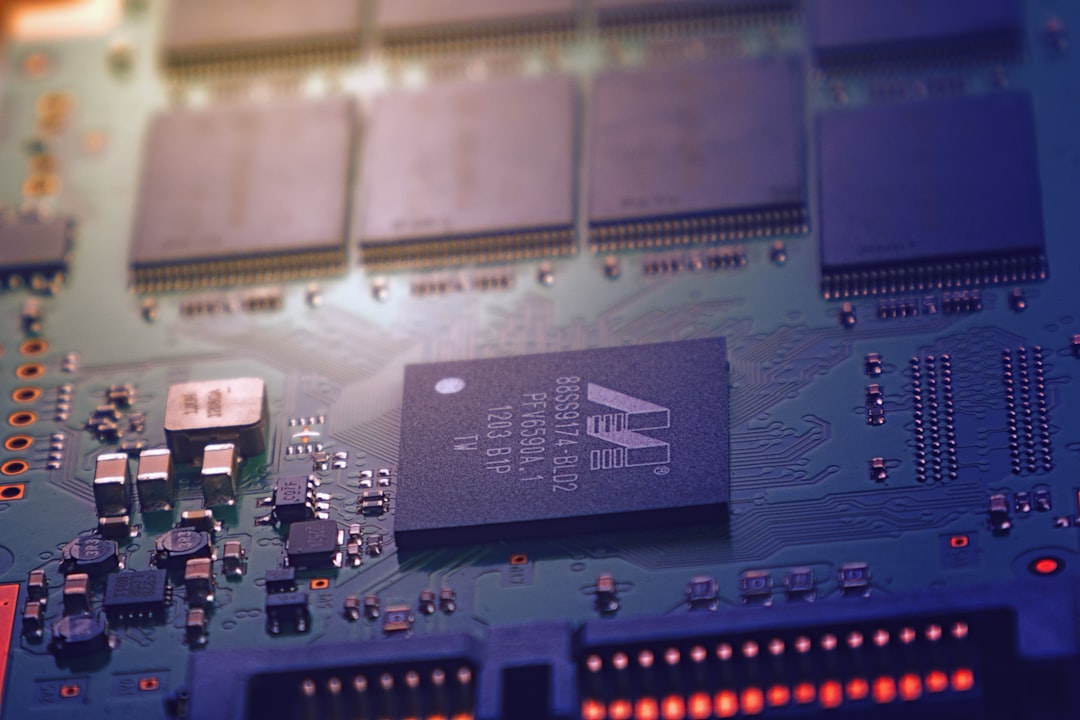
I've been enjoying a new e-mail newsletter by James Bowman of Excamera Labs. James is the creator behind awesome electronics projects like the Gameduino 2, a full colour touchscreen for Arduino.
He has a bunch of new projects at the moment, like the SPIDriver that let's you connect to SPI devices from your computer. And some of these projects he is building at home, as he explains in the latest edition of the newsletter:
For short-run through-hole PCB assembly, there's not much point in having these made abroad vs. making them yourself. Either way an 18-year-old with a soldering iron will be doing the work.
He pays his son $12 per hour for assembly and here is his argument on why it's a good thing:
It's also good just to get young people involved. Often when we're thinking of ways of introducing people to technology, we think of putting them in class. They already spend a lot of time in class! Much better to engage them in something practical and slightly unfamiliar. They seem to find it satisfying, and catching the inevitable failures gives them a hands-on insight into how things work.
I don't know what your high school work experiences were like, but I feel like maybe he's got a point. He goes on to explain how, due to Chinese manufacturers now selling directly online, getting electronic components doesn't have to be expensive. Buying 350 components of specific type would cost him $144 from a US distributor, while he could buy it directly from the Chinese manufacturer for $15.
In an earlier edition of the newsletter he describes how to make a “placement stencil” using a laser cutter, which makes it very easy to place components on a PCB by hand. Stencils for applying soldering past are also cheap nowadays, and you could get an IR reflow oven for a reasonable price as well.
In short, if you're making hundreds (instead of thousands) of something, it may just be easier and cheaper to do it yourself, even if said something is electronics.
#Electronics #Making
Comment on this post